Welding Technology of Natural Gas Pipeline
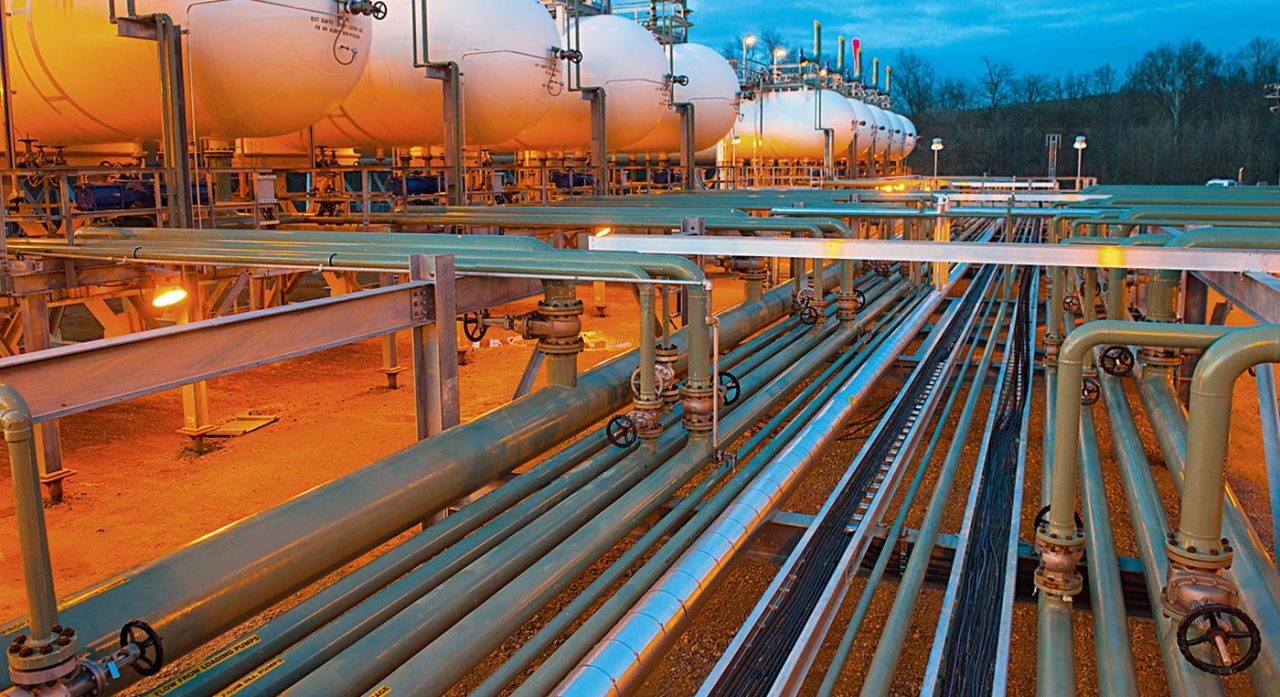
Introduction
Natural gas pipelines play a critical role in safely transporting vast volumes of this important energy resource over long distances from production fields to consumers. As an essential infrastructure, gas pipelines require sophisticated design and construction to withstand pressures up to 1400 psi for decades. However, one of the most important yet intricate operations is welding – the process of joining pipes together in a seamless, gas-tight fashion. This comprehensive report examines various welding technologies and methods used in natural gas pipelines, exploring their advantages/limitations, quality control aspects, and future prospects to ensure reliable transport of clean fuel into the future.
Welding Processes
A variety of welding processes have been developed and applied within the natural gas pipeline industry. The most prevalent include:
Shielded Metal Arc Welding (SMAW): Manual process using a consumable electrode within a shielding gas to create welds. Used for small diameter gathering lines but labor intensive. Tends to produce higher amounts of slag inclusions.
Gas Metal Arc Welding (GMAW): Semiautomatic process using a continuous wire feed and shielding gas. Operates at high deposition rates well suited for larger diameter pipelines. Requires less operator skill but quality depends on multitude of variables.
Flux-Cored Arc Welding (FCAW): Similar to GMAW but uses a special electrode containing powdered flux. Self-shielded variant (FCAW-G) provides good penetration in all positions. Prone to lack-of-fusion defects if parameters aren’t optimized.
Submerged Arc Welding (SAW): Highly productive automatic process using granular flux that melts and shields the weld puddle. Primary method for large diameter trunkline girth welds. Tolerates less-than-ideal conditions but creates more slag residual.
Electrogas Welding (EGW): Unique process using an arc and additional high velocity shielding gas for exceptional weld quality. Used where critical applications demand highest strength and fewest imperfections. Relatively new with higher capital costs.
Each process trades productivity for quality, and meeting natural gas pipeline inspection standards requires optimal procedure qualification. Ongoing research explores advanced variants like pulsed current GMAW for even smoother welds.
Welding Procedures and Consumables
Developing standardized welding procedures involves methodically qualifying parameters like current, voltage, wire feed speed, shielding gas composition, and tracking machine/operator performance. Major codes like CSA Z662 and ASME B31.8 provide guidance, while individual pipeline operators further refine in-house specifications.
Weld consumables must also undergo rigorous qualification examining mechanical properties and resistance to hydrogen embrittlement across the wide operating range from deep subzero to near critical temperatures. Approved filler metals include:
- Gas-shielded flux-cored wires for improved deposition rates in all positions
- Low hydrogen electrodes to minimize weld metal porosity and cracking susceptibility
- Nickel-alloy wires for sour gas or high-pressure applications approaching specified minimum yield strengths
Strict traceability ensures each heat lot satisfies charpy impact and chemical composition targets specified in acceptance standards. Overall, robust procedure and consumable qualification underpins welding reliability.
Welding Variables and Control
In the field, numerous variables influence weld quality that operators constantly monitor and control. Paramount is joint fit-up, with proper root gap sizing and root face preparation techniques highly contributing to sound welds. Back purge requirements for gas-shielded processes reduce porosity as well. Control also means:
- Strict temperature controls during multi-pass welding to prevent hydrogen-assisted cracking
- Interpass cleaning methods between layers like wire brushing, grinding to remove slag
- Bevel preparation accuracy on pipe ends to produce full joint penetration
- Shielding gas purity and flow rates
- Voltage, current and travelers’ speed adjustments due to joint fit-up difficulties
On modern pipelines, automated and semi-automatic GMAW/FCAW machinery incorporates extensive sensing/feedback loops to maintain parameter consistency pipe-to-pipe. This aids in achieving a reproducible 95%+ quality level across hundreds of girth welds.
Welding Quality Control
Given risks associated with gas pipeline failures, verifying weld integrity represents a critical quality control function. Operators utilize a multi-stage approach combining non-destructive and destructive tests:
- Visual inspection examines weld surface and interface for defects
- Dye-penetrant testing of root and final pass evaluates surface-connected porosity
- Ultrasonic testing checks for laminar imperfections, lack of fusion, and cracks
- Radiographic testing detects sub-surface flaws
- Hydrotesting subjects welds to pressures well above operation to induce failure
- Tensile testing destructive samples verifies minimum strength exceeds code
- Macroetching examines fusion characteristics under microscopy
Data from these techniques informs corrective actions, leads to continual process refinement, and helps qualifying new mainline fusion-welded joints. emerging techniques like phased array UT and digital radiography also improve sensitivity and automation. Overall, a culture of rigorous quality assurance ensures natural gas pipelines fulfill their critical role safely for decades to come.
Future Outlook
While pipelines remain the most efficient method for bulk natural gas transport, research explores new frontiers to strengthen this vital energy infrastructure. Areas attracting focus include:
- Micro-alloyed and low-carbon novel high-strength steels to smaller diameter and enhanced design pressures
- Advanced automated and robotic welding platforms for deeper water deployments and remote field repairs
- Hydrogen embrittlement resistant aluminum and plastic composite pipe development
- New non-destructive techniques like acoustic emission monitoring and guided ultrasound waves
- Real-time digital weld monitoring coupled with closed-loop controls for defect elimination
- In-the-ditch automated inspection gauges propelled internally via gas pressure
- Expansion of super-alloys and dissimilar metal joining techniques for critical stations
Constant evolution of welding technologies, materials and inspection strategies will help natural gas pipelines safely meet 21st century energy demands for cities, industries and homes across continents. Robust regulations, training, and partnership across industries sustains this progress.
Conclusion
As the primary construction method joining hundreds of miles of steel pipe infrastructure transporting a key fuel, welding stands as a cornerstone technology within the natural gas pipeline industry. However, its repeatable and reliable execution requires diligent standardization, control, and quality assurance measures. This report provides a comprehensive overview of key welding processes, critical variables, testing protocols and advancement areas that form the foundation for these pipelines to endure decades of hazardous duties. Continued cooperation across disciplines will strengthen welding capabilities to support tomorrow’s clean energy needs.