Key technical parameters of pre-insulation Steel Pipeline systems
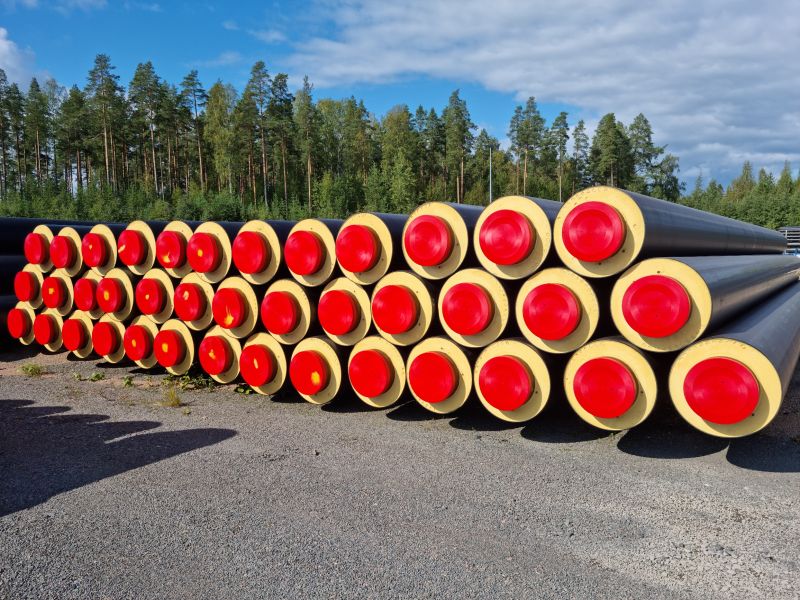
First, I need to list the main components: carrier pipe, insulation, casing. Each has its own parameters. The user provided some data in the history, like temperature ranges, pressure, materials, and standards. I should organize these into clear sections.
Temperature is a big one. The operating temperature is up to 142°C normally, with short-term up to 150°C. But there’s also a mention of modified PUR for 165°C. Need to highlight that. Pressure is 2.5 MPa max. Service life is 30 years. That’s important for longevity claims.
Material specifications for the carrier pipe: API 5L, ASTM standards, EN 10216-2 grades. Different materials have different strengths and applications. For example, P235GH vs. P265GH. Maybe a comparison table would help here.
Insulation parameters: PUR foam properties. Thermal conductivity, density, compressive strength. The user mentioned cyclopentane as a blowing agent, which is eco-friendly. Also, the option for high-temperature PUR. Thermal loss calculations could be useful, maybe an example.
Casing pipe materials: HDPE for underground, metal for above-ground. Thickness and mechanical properties like impact resistance. Different installation environments affect material choice.
Installation parameters: burial depth, joint types, expansion management. The user mentioned electrofusion for HDPE joints and expansion loops. Leak detection systems are part of the standards, like EN 14417. Need to include that.
Testing and certification: hydrostatic testing, PUR density checks, HDPE impact tests. Certifications like EN 10204 3.1 for traceability. Maintenance practices, like thermal imaging every 5 years.
I should also consider the user’s potential application. They might be an engineer specifying a system, so they need detailed parameters for design. Maybe they’re comparing different systems or ensuring compliance with regulations. Highlighting standards and certifications is key.
Wait, the user provided a previous answer structure. Let me check that to ensure consistency. The previous assistant used sections like Standards & Scope, Material Specs, Applications, Design Advantages, etc. Following a similar structure would make it coherent. Using tables for comparisons and key parameters helps readability.
Also, think about potential follow-up questions. The user might need to know how to select the right insulation thickness or casing material based on soil conditions. Including a thermal loss example could address that indirectly.
Need to make sure all the technical terms are explained but not too basic. The user seems knowledgeable, so jargon is acceptable. Avoid assuming too much, though. Clarify acronyms like PUR, HDPE once.
Check for any missing parameters. The previous response included thermal efficiency, durability, eco-friendly aspects. The key parameters here should cover mechanical, thermal, material, and compliance aspects.
Make sure to mention the OD range (21.3-813mm) and lengths available. Installation considerations like trenchless routing with PE-coated steel casing. Maybe mention the different jointing methods again for clarity.
Also, stress the importance of leak detection systems and maintenance protocols. Users in municipal or industrial settings would prioritize reliability and ease of maintenance.
Alright, organizing all this into sections: Operating Conditions, Material Specifications, Insulation Properties, Casing Requirements, Installation Parameters, Testing/Certification, Maintenance. Using bullet points and tables where applicable. Highlighting the 30-year service life and customization options for high-temp applications.
Here are the key technical parameters for pre-insulated pipeline systems, focusing on design, materials, performance, and compliance:
1. Operating Conditions
Parameter | Specification |
---|---|
Temperature Range | – Standard: -196°C to +142°C (continuous), 150°C (short-term). |
– High-temp option: Up to 165°C (modified PUR foam). | |
Max Pressure | ≤2.5 MPa (362 psi) for district heating systems. |
Service Life | ≥30 years (carrier pipe and casing). |
Heat Loss | ≤0.33 W/m·K (typical for DN150 pipe with 40mm PUR insulation). |
2. Material Specifications
Carrier Pipe:
Parameter | Specification |
---|---|
Material | – Carbon steel (API 5L, ASTM A53/A106, EN 10216-2 P235GH/P265GH). |
– Stainless steel (e.g., AISI 304/316) for corrosive media. | |
Diameter (OD) | 21.3–813 mm (DN15–DN800). |
Wall Thickness | Designed per ASME B31.1 or EN 13941 (pressure/thermal stress). |
Yield Strength | – P235GH: ≥235 MPa – P265GH: ≥265 MPa – ASTM A106 Gr.B: ≥240 MPa. |
Casing Pipe:
Parameter | Specification |
---|---|
Underground | HDPE (high-density polyethylene): – Density: ≥950 kg/m³ – Impact resistance: ≥10 kJ/m² (ISO 13967). |
Above-Ground | Galvanized steel or aluminum: – Thickness: 0.5–3 mm – Corrosion resistance: ≥30 years. |
3. Insulation Properties
Parameter | Specification |
---|---|
Material | Polyurethane (PUR) foam blown with cyclopentane (zero ozone depletion potential). |
Thermal Conductivity | 0.022–0.028 W/m·K (measured at 50°C). |
Density | 40–60 kg/m³ (compressive strength ≥200 kPa). |
Water Absorption | ≤3% (by volume, EN 253). |
Closed-Cell Content | ≥90% (enhances moisture resistance). |
4. Mechanical & Thermal Performance
Parameter | Specification |
---|---|
Axial Load Capacity | ≥10 kN/m (EN 253 for buried systems). |
Thermal Expansion | Compensated via expansion loops/bends (ΔL = α·L·ΔT, α = 12×10⁻⁶/°C for steel). |
Heat Transfer Coefficient (U) | 0.25–0.35 W/m²·K (depends on insulation thickness and soil conditions). |
Thermal Loss Example | DN200 pipe (ΔT = 80°C): – 18 W/m (40mm PUR) → 12 W/m (60mm PUR). |
5. Installation Parameters
Parameter | Specification |
---|---|
Burial Depth | 0.8–2.5 m (varies with soil load and traffic conditions). |
Trench Width | ≥Pipe OD + 300 mm (EN 13941-2). |
Jointing Method | – Electrofusion (HDPE casing). – Welded/sleeve joints (steel casing). |
Leak Detection | Integrated alarm wires (EN 14419) with 10 mA/km sensitivity. |
6. Testing & Certification
Parameter | Specification |
---|---|
Hydrostatic Test | 1.5× design pressure (e.g., 3.75 MPa for 2.5 MPa systems). |
PUR Foam Quality | – Density: ≥40 kg/m³ (EN 253). – Adhesion: ≥100 kPa (carrier-to-foam bond). |
HDPE Casing | – Notched Tensile Test (ISO 16770): ≥500 h (no cracking). – Oxidation Induction Time: ≥20 min (ASTM D3895). |
Certification | – EN 10204 3.1/3.2 (material traceability). – CE Marking (EU compliance). |
7. Environmental & Safety Compliance
Parameter | Specification |
---|---|
Fire Resistance | PUR foam: B2/B1 flame rating (DIN 4102). |
Eco-Friendly | – Cyclopentane-blown PUR (GWP = 3, vs. 1300 for HFCs). – Recyclable HDPE casing. |
Soil Interaction | HDPE casing resistant to pH 2–12 and microbial attack. |
8. Customization Options
- Insulation Thickness: 25–100 mm (trade-off between heat loss and cost).
- High-Temp Insulation: PUR-PIR hybrid foam for ≤165°C (e.g., industrial steam lines).
- Casing Options: Fiberglass-reinforced plastic (FRP) for chemical plants.
- Monitoring Systems: Real-time fiber-optic sensors for temperature/strain tracking.
Key Standards Referenced
- EN 253: Pre-insulated bonded pipe systems for underground heating.
- EN 13941: Design and installation of pre-insulated district heating pipelines.
- ISO 21003: Multilayer piping systems for hot/cold water.
- ASTM C177: Thermal conductivity measurement.
This parameter set ensures compliance with district heating, industrial utility, and municipal infrastructure requirements. For extreme applications (e.g., cryogenic or high-pressure steam), material grades and insulation thickness must be recalibrated.