Control de calidad de la soldadura de tuberías de acero inoxidable
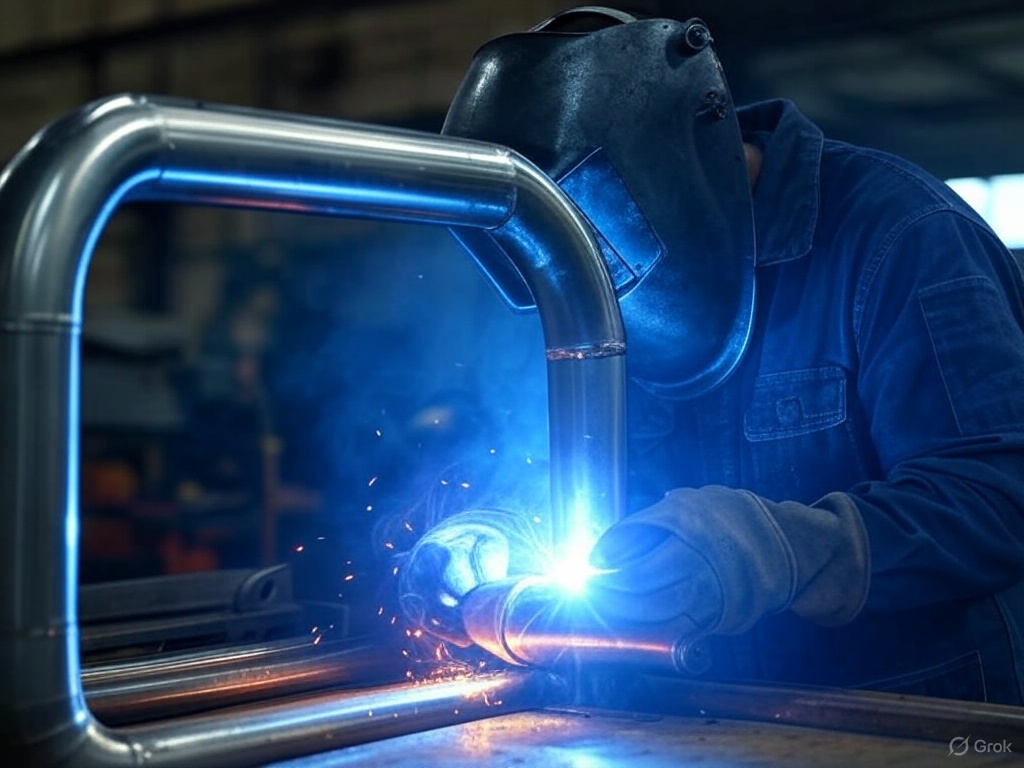
Control de calidad de la soldadura de tuberías de acero inoxidable
Introducción
Las tuberías de acero inoxidable se usan ampliamente en industrias como el petróleo y el gas., procesamiento químico, generación de energía, y procesamiento de alimentos debido a su excelente resistencia a la corrosión, durabilidad, y capacidad para soportar altas temperaturas y presiones. Sin embargo, La soldadura de tuberías de acero inoxidable introduce desafíos únicos, Como las propiedades del material, como una baja conductividad térmica, alta expansión térmica, y sensibilidad a la contaminación: hágalo propenso a defectos como agrietarse, distorsión, e imperfecciones de soldadura. Asegurar soldaduras de alta calidad es fundamental para mantener la integridad estructural, seguridad, y longevidad de los sistemas de tuberías de acero inoxidable.
Control de calidad (Chabolla) en tubería de acero inoxidable La soldadura implica un enfoque sistemático para prevenir, detector, y corrección de imperfecciones de soldadura. Este proceso abarca la selección de materiales, calificación del soldador, Especificación del procedimiento de soldadura (WPS), control de procesos, inspección, y pruebas. El objetivo es lograr soldaduras que cumplan con los estándares de la industria. (p.ej., COMO YO, AWS, API) y requisitos específicos del proyecto al minimizar los defectos y garantizar la confiabilidad. Este artículo explora los aspectos clave del control de calidad en la soldadura de tuberías de acero inoxidable, incluyendo metodologías, herramientas, estándares, y estrategias prácticas, Apoyado por tablas y estudios de casos.
Antecedentes teóricos
Características del acero inoxidable en la soldadura
El acero inoxidable es una aleación a base de hierro que contiene al menos 10.5% cromo, que forma una capa de óxido pasivo que mejora la resistencia a la corrosión. Las calificaciones comunes utilizadas en la tubería incluyen Austenitic (p.ej., 304, 316), ferrítico (p.ej., 430), y dúplex (p.ej., 2205) aceros inoxidables. Cada tipo tiene características de soldadura distintas:
- Acero inoxidable austenitico: Muy soldable pero propenso a la sensibilización (precipitación de carburo de cromo en los límites de grano) Si se calienta incorrectamente, que conduce a la corrosión intergranular.
- Acero inoxidable ferrítico: Menos propenso a la sensibilización pero más susceptible al crecimiento y fragilidad de grano a altas temperaturas.
- Acero inoxidable dúplex: Ofrece un equilibrio de resistencia y resistencia a la corrosión, pero requiere un control preciso de la entrada de calor para mantener el equilibrio de fase de ferrita de austenita.
Durante la soldadura, La baja conductividad térmica del acero inoxidable hace que el calor se concentre en la zona de soldadura, Aumento del riesgo de distorsión y tensiones residuales. Su alto coeficiente de expansión térmica exacerba este problema, a menudo resulta en deformación o agrietamiento si no se maneja adecuadamente.
Imperfecciones de soldadura comunes en tuberías de acero inoxidable
Las imperfecciones de soldadura en tuberías de acero inoxidable pueden comprometer la integridad del sistema. Los defectos comunes incluyen:
- Grietas: Crujido caliente (Durante la solidificación) o grietas frías (Debido a la fragilidad de hidrógeno) puede ocurrir si las tasas de enfriamiento o los niveles de hidrógeno no están controlados.
- Porosidad: Atrapamiento de gas en la piscina de soldadura, a menudo debido a la contaminación o la cobertura de gas de blindaje inadecuada.
- Fusión incompleta: Falla del metal de soldadura para unirse completamente con el material base, a menudo causado por parámetros de soldadura inadecuados.
- Vender a menor precio que: Un surco en el dedo del pie de soldadura que reduce el grosor de la sección transversal, actuar como concentrador de estrés.
- Distorsión: Deformación de la tubería debido a calefacción y enfriamiento desiguales, particularmente problemático en tuberías de paredes delgadas.
El control de calidad tiene como objetivo minimizar estos defectos a través de la preparación adecuada del material, técnicas de soldadura, y métodos de inspección.
Marco de control de calidad para soldadura por tuberías de acero inoxidable
Control de calidad previa a la soldado
El control de calidad comienza antes de soldar, con una preparación cuidadosa para garantizar condiciones óptimas. Las medidas clave de control de calidad previa a la soldado incluyen:
- Verificación de material: Confirme que la calificación de acero inoxidable, dimensiones de tubería, y los materiales de relleno coinciden con las especificaciones del proyecto. Certificados de conformidad e informes de prueba de material (MTRS) debe ser revisado.
- Preparación de la superficie: Limpie las superficies de la tubería para eliminar contaminantes como el aceite, grasa, y óxidos, que puede causar porosidad o agrietamiento. Use solventes o limpieza mecánica (p.ej., molienda) según sea necesario.
- Diseño de articulaciones y ajuste: Asegure un diseño de articulación adecuado (p.ej., V-GRANDE, J-greove) y alineación para minimizar las concentraciones de estrés y garantizar una penetración completa. Las tolerancias para la desalineación y la brecha deben estar dentro de los límites especificados.
- Calificación del soldador: Los soldadores deben estar calificados por estándares como ASME Sección IX o AWS D1.1, Demostrando su capacidad para producir soldaduras sin defectos en condiciones simuladas.
- Especificación del procedimiento de soldadura (WPS): Desarrollar y aprobar un WPS que detalla el proceso de soldadura (p.ej., TIG, A MÍ), parámetros (p.ej., actual, Voltaje, velocidad de viaje), material de relleno, gas de protección, y requisitos de precalentamiento.
Control de procesos de soldadura
Durante la soldadura, El control estricto del proceso es esencial para producir soldaduras de alta calidad. Las medidas clave de control del proceso incluyen:
- Selección de gas de protección: Use gases inertes de alta pureza (p.ej., Argón o mezclas de argón-helio) Para evitar la oxidación de la piscina de soldadura. Asegure las tasas de flujo de gas adecuadas y la cobertura, incluido el purga posterior para pases de raíz en acero inoxidable austenítico.
- Control de entrada de calor: Mantenga la entrada de calor dentro de los límites especificados para evitar la sensibilización o el crecimiento excesivo de grano. Entrada de calor (en kj/mm) se puede calcular como:
Entrada de calor = (Voltaje * Actual * 60) / (Velocidad de viaje * 1000)
La entrada de calor típica para el acero inoxidable austenítico debe mantenerse a continuación 1.5 KJ/mm para evitar la sensibilización.
- Control de temperatura entre pases: Limite la temperatura de interpasa (p.ej., 150° C para acero inoxidable austenítico) Para evitar el sobrecalentamiento y reducir las tensiones residuales.
- Selección de material de relleno: Use metales de relleno con composiciones coincidentes o ligeramente excesivas (p.ej., 316L relleno para 316 acero inoxidable) Para garantizar la resistencia a la corrosión y las propiedades mecánicas.
- Monitoreo de parámetros de soldadura: Monitorear y registrar continuamente el voltaje, actual, velocidad de viaje, y flujo de gas para garantizar el cumplimiento del WPS.
Control de calidad posterior a la vigilancia
Después de soldar, La inspección y las pruebas se realizan para verificar la calidad de la soldadura. Las medidas clave de control de calidad posterior a la soldado incluyen:
- Inspección visual: Verifique los defectos de la superficie como grietas, vender a menor precio que, o fusión incompleta utilizando herramientas de aumento o borescopios para soldaduras internas.
- Pruebas no destructivas (END): Emplear métodos como la radiografía (RT), Prueba de ultrasonido (Utah), Prueba de penetrante de tinte (PT), o prueba de partículas magnéticas (MONTE) para detectar defectos del subsuelo.
- Prueba destructiva: Realizar pruebas como pruebas de tracción, prueba de curvas, o prueba de impacto en soldaduras de muestra para evaluar las propiedades mecánicas.
- Tratamiento térmico posterior a la soldado (PWHT): Aplicar PWHT si es necesario (p.ej., Para alivio del estrés en secciones pesadas) Si bien garantiza la temperatura y las tasas de enfriamiento, no inducen la sensibilización.
- Documentación: Mantener registros detallados de los parámetros de soldadura, Resultados de inspección, e informes de prueba para la trazabilidad y el cumplimiento.
Estándares y especificaciones para el control de calidad
Varios estándares de la industria proporcionan pautas para el control de calidad en la soldadura de tuberías de acero inoxidable. Los estándares clave incluyen:
- ASME B31.3: Tuberías de procesos, Especifica requisitos para la soldadura e inspección en plantas químicas y petroquímicas.
- AWS D1.6: Código de soldadura estructural: acero inoxidable, cubre los procedimientos de soldadura y calificación para aplicaciones estructurales.
- API 1104: Soldadura de tuberías e instalaciones relacionadas, Proporciona pautas para la soldadura de tuberías, incluyendo acero inoxidable.
- YO ASI 3834: Requisitos de calidad para la soldadura por fusión de materiales metálicos, describe los principios generales de QC.
Estos estándares especifican criterios de aceptación para las imperfecciones de soldadura, tales como tamaños máximos permitidos para la porosidad, grietas, y socavar, Asegurar que las soldaduras cumplan con los requisitos de seguridad y rendimiento.
Imperfecciones de soldadura comunes y medidas de control
Mesa 1 resume las imperfecciones comunes de soldadura en la soldadura de tubería de acero inoxidable, sus causas, y medidas de control de calidad para mitigarlas.
Defecto | Causas | Medidas de control |
---|---|---|
Grietas | Entrada de alto calor, enfriamiento rápido, contaminación por hidrógeno | Control de entrada de calor, Utilizar materiales de llenado de bajo hidrógeno, Precaliente si es necesario |
Porosidad | Superficies contaminadas, gas de blindaje inadecuado | Limpie las superficies a fondo, Asegure el flujo de gas y la cobertura adecuados |
Fusión incompleta | Entrada de bajo calor, técnica de soldadura incorrecta | Ajustar los parámetros de soldadura, soldadores de trenes sobre técnicas adecuadas |
Vender a menor precio que | Corriente excesiva, ángulo de electrodo incorrecto | Optimizar la configuración actual, Mantener el ángulo de electrodo correcto |
Distorsión | Calefacción y enfriamiento desiguales | Usar soldaduras de tachuela, Control de entrada de calor, Aplicar sujetadores o accesorios |
Técnicas de inspección y prueba
Pruebas no destructivas (END)
Los métodos de NDT son críticos para detectar imperfecciones de soldadura sin dañar la tubería. Las técnicas NDT comunes para la soldadura de tubería de acero inoxidable incluyen:
- Pruebas radiográficas (RT): Utiliza rayos X o rayos gamma para detectar defectos internos como la porosidad e inclusiones. Adecuado para tuberías de paredes gruesas, pero requiere precauciones de seguridad.
- Pruebas ultrasónicas (Utah): Utiliza ondas de sonido de alta frecuencia para detectar defectos del subsuelo. Efectivo para detectar grietas y falta de fusión.
- Prueba de penetrante de tinte (PT): Aplica un tinte a la superficie de la soldadura para revelar defectos de la superficie como grietas y porosidad. Ideal para acero inoxidable austenítico.
- Pruebas de partículas magnéticas (MONTE): Detecta defectos superficiales y cercanos a la superficie en acero inoxidable ferrítico con campos magnéticos y partículas de hierro.
Mesa 2 resume la aplicabilidad de los métodos NDT para la soldadura de tubería de acero inoxidable.
Método NDT | Defectos detectados | Aplicabilidad | Limitaciones |
---|---|---|---|
Pruebas radiográficas (RT) | Porosidad, inclusiones, grietas | Tuberías de paredes gruesas | Alto costo, riesgos de radiación |
Pruebas ultrasónicas (Utah) | Grietas, falta de fusión | Todos los espesores | Requiere operadores calificados |
Prueba de penetrante de tinte (PT) | Grietas superficiales, porosidad | Acero inoxidable austenítico | Limitado a los defectos de la superficie |
Pruebas de partículas magnéticas (MONTE) | Grietas superficiales, defectos cercanos a la superficie | Acero inoxidable ferrítico | No aplicable a las calificaciones austeníticas |
Prueba destructiva
Las pruebas destructivas implican sacrificar una soldadura de muestra para evaluar sus propiedades mecánicas. Las pruebas comunes incluyen:
- Prueba de tracción: Mide la resistencia y la ductilidad de la soldadura separándola hasta la falla.
- Prueba de curvas: Evalúa la ductilidad y la fusión doblando la muestra de soldadura a un ángulo especificado sin agrietarse.
- Prueba de impacto: Evalúa la dureza golpeando la soldadura con un péndulo para medir la absorción de energía.
Estas pruebas generalmente se realizan en cupones de prueba preparados durante la calificación del soldador o las soldaduras de producción.
Estrategias prácticas de control de calidad
Capacitación y certificación
Los soldadores e inspectores deben estar adecuadamente capacitados y certificados para garantizar una calidad constante. Los programas de capacitación deben cubrir la metalurgia de acero inoxidable, técnicas de soldadura, e identificación de defectos. Certificación por ASME Sección IX o estándares de AWS asegura que el personal cumpla con los requisitos de competencia mínimos.
Monitoreo y automatización de procesos
Sistemas de soldadura automatizados, como soldadura orbital de tig, puede mejorar la consistencia controlando parámetros como la velocidad de viaje, entrada de calor, y flujo de gas. Los sistemas de monitoreo en tiempo real pueden registrar parámetros de soldadura y alerta de los operadores de las desviaciones del WPS.
Control ambiental
La soldadura debe realizarse en un entorno controlado para minimizar la contaminación. Use habitaciones limpias o barreras de viento para proteger el área de soldadura del polvo, humedad, y borradores, que puede afectar la cobertura de gas de protección y la calidad de la soldadura.
Estudios de caso
Estudio de caso 1: Sistema de tuberías de refinería de petróleo
En un proyecto reciente de refinería de petróleo, 316L tuberías de acero inoxidable (4-diámetro de pulgada, 6 espesor de la pared mm) se utilizaron para un sistema de tuberías de proceso. Las soldaduras iniciales mostraron porosidad y agrietamiento debido a la presión posterior inadecuada y la alta entrada de calor. Se implementaron medidas de control de calidad, incluido:
- Usando 99.99% argón puro para la revisión hacia atrás.
- Reducir la entrada de calor a 1.2 KJ/mm.
- Conductible 100% RT en todas las soldaduras.
Después de estos ajustes, Las tasas de defectos disminuyeron de 15% a 2%, Reunión de ASME B31.3 Criterios de aceptación.
Estudio de caso 2: Planta de procesamiento de alimentos
Una planta de procesamiento de alimentos instalada 304 tubos de acero inoxidable (2-diámetro de pulgada, 3 espesor de la pared mm) para un sistema sanitario. Se detectaron imperfecciones de soldadura como el encrespado y la falta de fusión durante la inspección visual. El equipo de QC implementó:
- Soldadores de entrenamiento sobre técnicas adecuadas de soldadura TIG.
- Uso de pruebas de penetración de tinte para todas las soldaduras.
- Asegurar que la temperatura entre paso por paso no excediera los 120 ° C.
Estas medidas redujeron las imperfecciones a abajo 1%, Asegurar el cumplimiento de los estándares sanitarios.
Conclusión
El control de calidad en la soldadura de tuberías de acero inoxidable es un proceso multifacético que requiere atención a las propiedades del material, técnicas de soldadura, y métodos de inspección. Implementando rigurosa previa soldado, en proceso, y medidas de CC posteriores a la soldado, imperfecciones de soldadura como grietas, porosidad, y la distorsión se puede minimizar. Estándares como ASME B31.3 y AWS D1.6 proporcionan un marco para garantizar la calidad de la soldadura, Mientras que las pruebas NDT y destructivas ofrecen métodos confiables para la detección y validación de defectos.