Manufacturing Processes of Alloy Steel Pipe
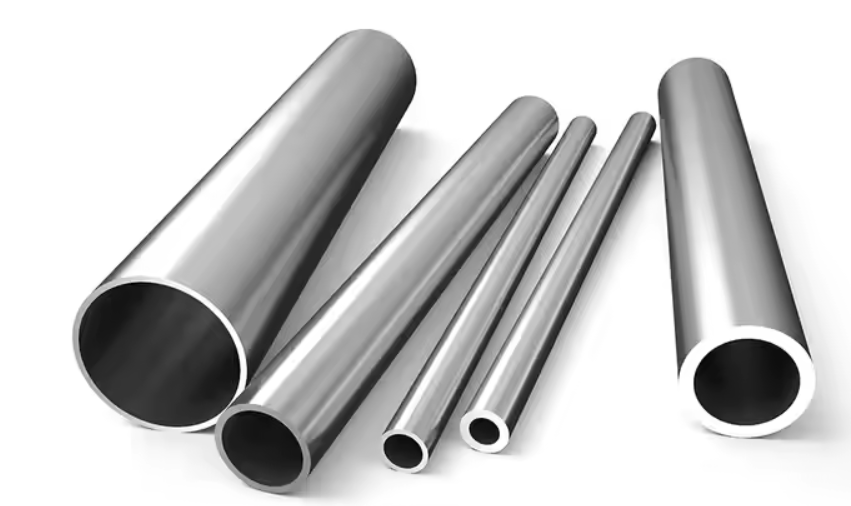
Manufacturing Processes of Alloy Steel Pipes
Introduction
Alloy steel pipes are integral components in various industries, including oil and gas, power generation, and construction. Their enhanced mechanical properties, such as increased strength, toughness, and resistance to wear and corrosion, make them suitable for demanding applications. This article explores the manufacturing processes of alloy steel pipes, highlighting the techniques used to achieve the desired properties and dimensions.
1. Raw Material Selection
The manufacturing process begins with the selection of high-quality raw materials. Alloy steel is composed of iron, carbon, and other alloying elements such as chromium, molybdenum, nickel, and vanadium. These elements are added in specific proportions to enhance the steel’s mechanical and chemical properties.
- Chromium: Increases corrosion resistance and hardness.
- Molybdenum: Enhances strength and high-temperature stability.
- Nickel: Improves toughness and impact resistance.
- Vanadium: Increases strength and wear resistance.
2. Melting and Casting
2.1 Melting
The selected raw materials are melted in an electric arc furnace (EAF) or a basic oxygen furnace (BOF). The melting process involves heating the materials to a high temperature, allowing them to combine and form a homogeneous liquid alloy.
- Electric Arc Furnace (EAF): Uses electrical energy to melt scrap steel and alloying elements. It offers precise control over the composition and temperature of the molten steel.
- Basic Oxygen Furnace (BOF): Utilizes pure oxygen to convert molten iron and scrap steel into alloy steel. It is known for its efficiency and high production rates.
2.2 Casting
Once the alloy is melted, it is cast into solid forms, typically using continuous casting or ingot casting methods.
- Continuous Casting: The molten steel is poured into a water-cooled mold, where it solidifies into a continuous slab or billet. This method is efficient and produces high-quality steel with minimal defects.
- Ingot Casting: The molten steel is poured into molds to form ingots. This traditional method is used for producing large sections of steel, which are later rolled or forged into pipes.
3. Forming Processes
After casting, the solid steel is formed into pipes using various techniques, such as seamless and welded pipe manufacturing.
3.1 Seamless Pipe Manufacturing
Seamless pipes are produced without a welded seam, providing superior strength and reliability. The process involves several steps:
- Piercing: A solid billet is heated and pierced using a rotary piercing mill to create a hollow shell.
- Elongation: The hollow shell is elongated using a mandrel mill or plug mill, reducing its wall thickness and increasing its length.
- Sizing: The elongated pipe is passed through a sizing mill to achieve the desired dimensions and surface finish.
3.2 Welded Pipe Manufacturing
Welded pipes are produced by forming a flat strip or plate into a cylindrical shape and welding the edges together. The process includes:
- Forming: The steel strip or plate is bent into a cylindrical shape using a roll forming or press forming machine.
- Welding: The edges of the formed cylinder are welded together using techniques such as electric resistance welding (ERW) or submerged arc welding (SAW).
- Finishing: The welded pipe is heat-treated and subjected to various finishing processes to enhance its mechanical properties and surface quality.
4. Heat Treatment
Heat treatment is a critical step in the manufacturing process, enhancing the mechanical properties of alloy steel pipes. The process involves heating the pipes to a specific temperature and then cooling them at a controlled rate.
- Annealing: The pipes are heated to a high temperature and then slowly cooled to relieve internal stresses and improve ductility.
- Quenching and Tempering: The pipes are heated to a high temperature and then rapidly cooled (quenched) to increase hardness. They are then reheated (tempered) to achieve the desired balance of strength and toughness.
5. Finishing and Inspection
After heat treatment, the pipes undergo various finishing processes to achieve the final dimensions and surface quality. These processes include:
- Straightening: The pipes are straightened using a straightening machine to ensure uniformity and alignment.
- Cutting: The pipes are cut to the desired length using saws or cutting machines.
- Surface Treatment: The pipes are subjected to surface treatments such as pickling, coating, or painting to enhance corrosion resistance and appearance.
6. Quality Control and Testing
Rigorous quality control measures are implemented to ensure the integrity and performance of alloy steel pipes. This includes non-destructive testing, dimensional inspection, and mechanical testing.
- Non-Destructive Testing (NDT): Techniques such as ultrasonic testing and radiography are used to detect internal defects or discontinuities.
- Dimensional Inspection: Ensures the pipes meet the precise dimensions and tolerances specified in industry standards.
- Mechanical Testing: Evaluates the tensile, yield, and impact strength of the pipes to ensure they meet the required specifications.