pre-insulated Steel pipe : EN 253, EN 448, EN 488 and EN 489 European standards
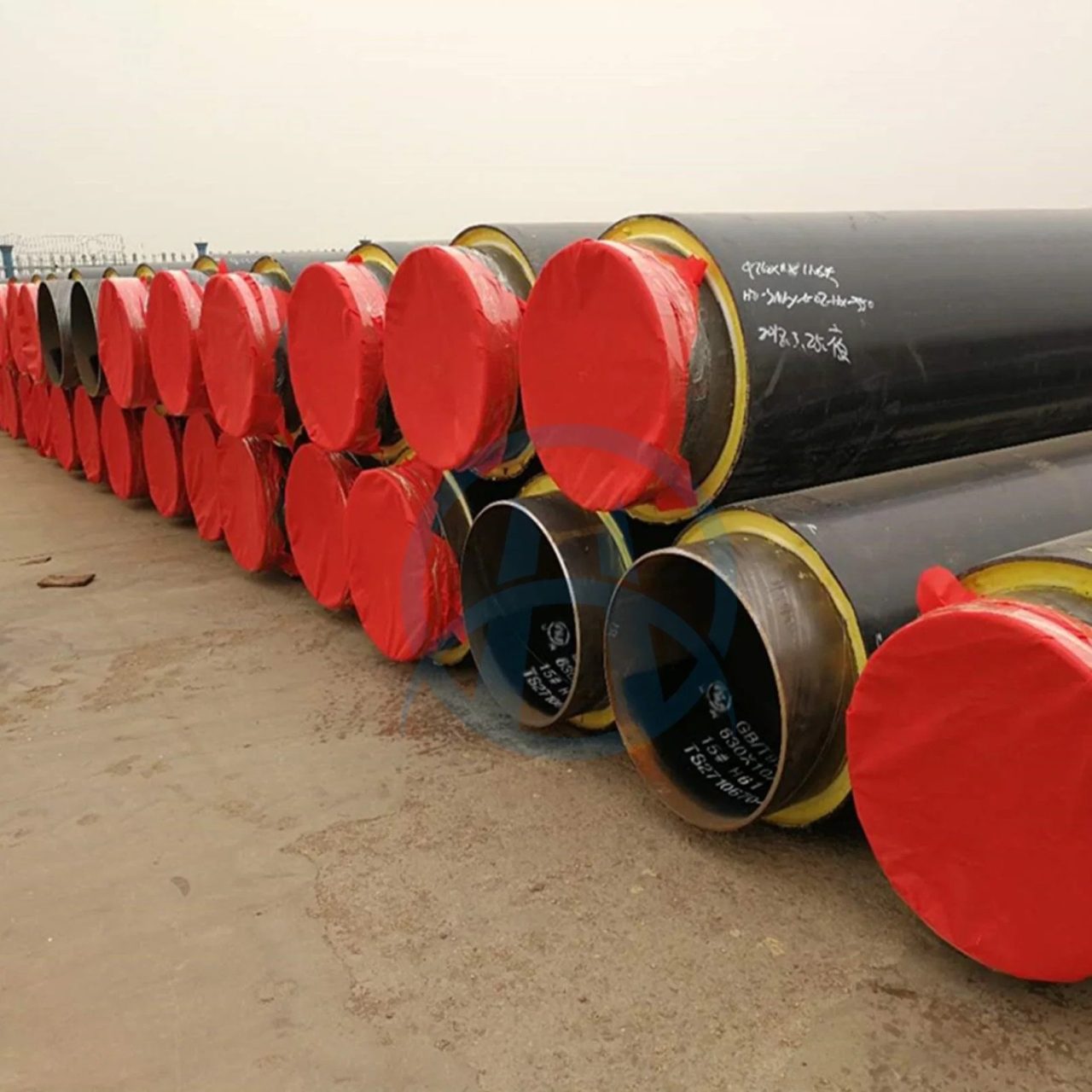
Specific contents of EN 253, EN 448, EN 488, EN 489 standards
The specific contents of EN 253, EN 448, EN 488 and EN 489 standards are as follows:
- In 253 :
- Standard name: Regional heating pipelines – bonded single pipe system for direct buried hot water networks – factory-made steel pipe components, polyurethane insulation materials and casing polyethylene.
- Main content: This standard specifies the specific requirements for single-tube bonding systems used in direct buried hot water pipe networks, including factory-made steel water supply pipe fitting components, polyurethane insulation materials and shell polyethylene.
- In 448 :
- Standard name: Regional heating pipes – Single pipe bonding system for direct buried hot water networks – Factory-made steel water supply pipe fitting components, polyurethane insulation and shell polyethylene.
- Main content: This standard describes in detail the specific requirements of a single-tube bonding system used in direct buried hot water pipe networks, including factory-made steel water supply pipe fitting components, polyurethane insulation materials and shell polyethylene.
- In 488 :
- Standard name: Regional heating pipes – Single pipe bonding system for direct buried hot water networks – Factory-made steel water supply pipe fitting components, polyurethane insulation and shell polyethylene.
- Main content: This standard specifies the specific requirements for single-tube bonding systems used in direct buried hot water pipe networks, including factory-made steel water supply pipe fitting components, polyurethane insulation materials and shell polyethylene.
- In 489 :
- Standard name: Regional heating pipes – Single and double pipe bonding system network for underground hot water – Part 1: Connecting casings and thermal insulation components of hot water networks comply with EN 13941-1.
- Main content: This standard specifies the specific requirements of single-pipe and double-pipe bonding systems for underground hot water, including the design, manufacturing and installation requirements of connecting sleeves and insulation components to ensure the safe and efficient operation of the heating system.
These standards mainly involve direct buried hot water pipe network systems for regional heating pipelines, covering all aspects from material selection to system design, manufacturing and installation, ensuring the reliability and safety of the system.
What is the specific content of EN 488 standard?
The specific content of the EN 488 standard mainly involves regional heating piping systems, especially pre-insulated connecting piping systems in direct buried hot water supply networks. This standard specifies the requirements and testing methods for polyurethane thermally insulated and polyethylene coated steel pipes for steel valve assemblies, and is suitable for continuous operation under a variety of conditions, including operating conditions with a minimum temperature of 4°C. According to EN 10204, all steel pipes, valves and steel components shall be provided with inspection certificate 3.1 when delivered to ensure compliance with the standard requirements. In addition, EN 488 covers the applications of polyurethane thermal insulation materials.
Specifically, the contents of the EN 488 standard include:
- Material requirements: Specifies the requirements for polyurethane thermal insulation and polyethylene outer coated steel pipes of steel valve components.
- Test Methods: Various testing methods are described in detail to ensure product performance and reliability under different conditions.
- Additional elements: The valve assembly may include additional elements such as measuring lines, gaskets and diffusion barriers.
- Certification requirements: All steel pipes, valves and steel components should be accompanied by inspection certificate 3.1 when delivered to ensure compliance with the standard requirements.
EN 488 standard is applicable to heating pipe manufacturers, valve manufacturers, design engineers, quality control personnel, and research and development facilities, and is committed to ensuring the safety and reliability of regional heating pipe systems.
API 5L, ASTM A53/A106/A333, EN 10216-2 Technical requirements for P235GH/P265GH standard
The technical requirements of API 5L, ASTM A53/A106/A333 and EN 10216-2 P235GH/P265GH standards are as follows:
The fire 5L
- Scope of application: Mainly used in oil, natural gas and industrial pipelines, suitable for transporting oil, natural gas and water.
- Level: including B, X42, X52, etc. Different levels correspond to different strength and toughness requirements.
- Test requirements: Including non-destructive testing (NDT), chemical composition analysis and mechanical performance testing.
- Temperature range: Suitable for general use, but not for high temperature applications.
- Connection method: Seamless and welded steel pipes.
- Application: Mainly used for pipelines for transporting hydrocarbons from a long distance.
ASTM A53/A106/A333
- ASTM A53:
- Scope of application: Suitable for mechanical and pressure applications such as pipes and HVAC systems.
- Chemical composition: The specific composition is not listed in detail, but the materials that meet the ASTM A53 standard are usually carbon steel.
- Mechanical properties: including yield strength, tensile strength, elongation and impact test.
- Temperature range: Suitable for general use, but not for high temperature applications.
- Connection method: Seamless and welded steel pipes.
- Application: Widely used in construction, bridge and pipeline systems.
- ASTM A106:
- Scope of application: Suitable for high temperature applications and services such as refineries and power plants.
- Chemical composition: The specific composition is not listed in detail, but the materials that meet the ASTM A106 standard are usually carbon steel.
- Mechanical properties: including yield strength, tensile strength, elongation and impact test.
- Temperature range: Suitable for high temperature applications, up to 750°F (approximately 399°C).
- Connection method: seamless steel pipe.
- Application: Widely used in high temperature and high pressure pipeline systems.
- ASTM A333 :
- Scope of application: Suitable for low temperature applications, such as low temperature piping systems.
- Chemical composition: The specific composition is not listed in detail, but the materials that meet the ASTM A333 standard are usually carbon steel.
- Mechanical properties: including yield strength, tensile strength, elongation and impact test.
- Temperature range: Suitable for low temperature applications.
- Connection method: Seamless and welded steel pipes.
- Application: Widely used in low temperature pipeline systems.
EN 10216-2 P235GH/P265GH
- P235GH:
- Scope of application: Suitable for pressure purposes, such as boilers, heat exchangers and other pressure vessels.
- Chemical composition:
- C (carbon): ≤0.20%
- Si (silicon): ≤0.40%
- Mn (manganese): ≤1.20%
- P (phosphorus): ≤0.045%
- S (sulfur): ≤0.045%
- Cr (chromium): 0.40% to 0.80%
- Ni (Mountain): ≤0.50%
- Mo (Sheet): ≤0.25%
- Cu (copper): ≤0.30%
- Al (aluminum): ≤0.015%
- Fe (iron) margin
- Mechanical properties:
- Yield strength: ≥415 MPa
- Tensile strength: ≥610 MPa
- Elongation: ≥16%
- Impact test: ≥24 J
- Temperature range: Suitable for high temperature applications.
- Connection method: seamless steel pipe.
- Application: Widely used in high temperature and high pressure pipeline systems.
- P265GH:
- Scope of application: Suitable for pressure purposes, such as boilers, heat exchangers and other pressure vessels.
- Chemical composition:
- C (carbon): ≤0.20%
- Si (silicon): ≤0.40%
- Mn (manganese): ≤1.20%
- P (phosphorus): ≤0.045%
- S (sulfur): ≤0.045%
- Cr (chromium): 0.80% to 1.50%
- Ni (Mountain): ≤0.50%
- Mo (Sheet): ≤0.25%
- Cu (copper): ≤0.30%
- Al (aluminum): ≤0.015%
- Fe (iron) margin
- Mechanical properties:
- Yield strength: ≥415 MPa
- Tensile strength: ≥610 MPa
- Elongation: ≥16%
- Impact test: ≥24 J
- Temperature range: Suitable for high temperature applications.
- Connection method: seamless steel pipe.
- Application: Widely used in high temperature and high pressure pipeline systems.
Summarize
- API 5L is mainly used in oil, gas and industrial pipelines and is suitable for general purposes, but not for high temperature applications.
- ASTM A53/A106/A333 are suitable for mechanical and pressure applications, high temperature applications and low temperature applications, mainly carbon steel materials.
- EN 10216-2 P235GH/P265GH is suitable for pressure purposes such as boilers, heat exchangers and other pressure vessels, and is suitable for high temperature applications.
These standards have their own emphasis on chemical composition, mechanical properties and application scope, and must be matched according to the specific application scenario and requirements when choosing.
Thermal resistance and temperature limit of PUR foam insulation in pre-insulated steel pipes
The thermal resistance and temperature limitations of PUR foam insulation in pre-insulated steel pipes are as follows:
- Thermal resistance performance:
- The thermal conductivity of PUR foam is 0.023 W/m·K at -20°C and 0.028 W/m·K at +50°C, showing excellent thermal insulation performance.
- The λ value of PUR foam is 0.022 at -20°C and 0.027 at +50°C, which meets the functional requirements of EN 253.
- PUR foam has low thermal conductivity, which can effectively reduce heat loss and improve the overall performance of the system.
- Temperature limit:
- The temperature range of PUR foam is -200°C to +140°C and can be used with mineral wool up to +250°C.
- In practical applications, the maximum operating temperature of PUR foam is usually not exceeding 140°C, and generally below 120°C.
- In low temperature environments, PUR foam can still maintain good insulation performance and is suitable for extremely low temperature application scenarios.
To sum up, PUR foam has excellent thermal resistance performance and a wide range of temperature application in pre-insulated steel pipes, and can maintain a stable insulation effect under extreme temperature conditions.
In high temperature and high pressure scenarios, carrier tubes of different materials have different applicability. The following is an analysis of the suitability of several common materials for pipes in high temperature and high pressure environments:
- Stainless steel pipe:
- Advantages: Stainless steel pipes have excellent corrosion resistance and high temperature resistance, and can operate stably in high temperature environments for a long time and are suitable for conveying corrosive media or in environments where high temperature work is required. Stainless steel pipes have high mechanical strength, wear resistance, long service life and low maintenance cost.
- Application scenarios: It is widely used in petroleum, chemical industry, electricity, ships and other fields, especially in environments that require corrosion resistance and high temperature resistance.
- Carbon steel pipe:
- Advantages: Carbon steel pipes have high strength and pressure resistance, and are suitable for the transportation of medium and high pressure media, such as long-distance pipeline transportation. Carbon steel pipes can also maintain good performance in high temperature and high pressure environments.
- Application scenarios: Commonly used for oil, natural gas and hydrogen energy transmission, especially in environments where high intensity and pressure resistance are required.
- Polyethylene (PE) tube:
- Advantages: Polyethylene pipes have good corrosion resistance and temperature resistance, and are suitable for general corrosive liquid media transportation. PE pipes are lightweight, easy to install, and relatively low-priced.
- Application scenario: Suitable for domestic water, hot and cold water transportation, and the transportation of some non-corrosive media.
- Polyvinyl chloride (PVC) tube:
- Advantages: PVC pipe has good corrosion resistance and temperature resistance, and is suitable for general corrosive liquid media transportation. PVC tubes are resistant to acid and alkali, but not strong oxidants.
- Application scenario: Suitable for petrochemical, pharmaceutical, food processing and other industries, especially in environments where corrosion resistance is required.
- Polytetrafluoroethylene (PTFE) tube:
- Advantages: PTFE tubes have excellent chemical stability and high temperature resistance, and can resist corrosion from almost all chemical media. PTFE tubes are suitable for the transportation of extremely high temperature and highly corrosive gases.
- Application scenarios: Widely used in chemical, pharmaceutical, food processing, electronics, automobile, aerospace and other industries.
- Compound tube:
- Advantages: Composite tubes combine the advantages of a variety of materials, such as steel frame polyethylene composite tubes (PE-RTs) have good temperature resistance and corrosion resistance, and are suitable for high temperature and high pressure environments.
- Application scenario: It is suitable for municipal engineering, construction, industry and other fields, especially in environments where high strength and corrosion resistance are required.
To sum up, in high temperature and high pressure scenarios, stainless steel pipes and carbon steel pipes are more suitable for their excellent high temperature and pressure resistance; polyethylene pipes and polyvinyl chloride pipes are suitable for the transportation of general corrosive media; Tetrafluoroethylene pipes are suitable for the delivery of extremely high temperatures and strongly corrosive gases; composite pipes combine the advantages of a variety of materials and are suitable for a variety of complex environments.
High-density polyethylene (HDPE) shell tubes have excellent protective performance in underground and above ground environments, and the specific performance is as follows:
- Corrosion resistance: HDPE materials have extremely high chemical corrosion resistance and can resist the corrosion of chemical media such as acids, alkalis, and salts, so that they remain stable in harsh environments and extend their service life.
- Waterproof performance: HDPE material has extremely low water air transmittance, which can effectively protect the internal structure from moisture, and is suitable for underground and underwater environments.
- Mechanical properties: HDPE has good flexibility and impact resistance, can remain stable under various terrain conditions, and is not prone to cracking or deformation.
- Convenient construction: HDPE pipes are light in weight, easy to install, no additional trench is required, and the construction cost is low, and it is suitable for direct buried or laid in trench.
- Environmental protection: HDPE materials are non-toxic and odorless, and do not promote the growth of algae, bacteria or fungi, and meet environmental protection requirements.
- Durability: HDPE pipes have a long service life, up to more than 30 years, and in some cases up to 100 years.
- Adaptability: HDPE pipelines can adapt to stress changes caused by temperature changes and terrain changes, ensuring the safe and stable operation of the system.
- Anti-seepage performance: The thickness of the HDPE film should not be less than 1.50mm. Protective layers, such as filament non-woven geotextile, should be installed on both sides to enhance the anti-seepage effect.
To sum up, high-density polyethylene shell tubes show excellent protective performance in both underground and above ground environments and are suitable for a variety of application scenarios, including municipal engineering, agricultural irrigation, industrial refrigeration, aerospace insulation and environmental protection projects.
Typical application scenarios and cases of pre-insulated pipes in regional heating systems include:
- Residential and commercial buildings:
- Park Lane Estates by Hastings: Polypipe pre-insulated thermal network tubes are used to connect remote air source heat pumps (ASHPs) to provide efficient heating for high-end residential areas. This system not only reduces noise, but also improves energy efficiency.
- Malaysia: Pre-insulated piping is widely used in hot water supply and regional heating systems, especially in new building renovation projects, and is favored for its lightness, ease of installation and low maintenance costs.
- Large public facilities:
- Vancouver Olympic Village: Urecon’s EN 253 pre-insulated pipeline network provides space heat and domestic hot water for buildings at the 2010 Vancouver Olympics.
- Stanford University: Transforming from a traditional steam distribution network to a modern hot water system, using Kingspan LOGSTOR EN 253 pre-insulated pipes.
- Industrial Applications:
- Postobon: In the Dockside Green project in Vancouver, Canada, a pre-insulated piping system combines solar and geothermal energy to provide cooling water for non-alcoholic beverage production.
- Industrial Cooling Water Transport: Postobon uses pre-insulated piping systems that combine solar and geothermal energy to provide cooling water for non-alcoholic beverage production.
- Higher Education Institutions:
- University of Rochester: Transforming from a traditional steam distribution system to a modern hot water system, using Kingspan LOGSTOR EN 253 pre-insulated pipes.
- Enmax District Energy Complex in Calgary, Alberta: Denmark Kingspan-based solution using pre-insulated piping systems.
- Sustainable Development Projects:
- Dockside Green Project in Vancouver: Combining wood waste, garbage and solar energy to achieve sustainable development through pre-insulated piping systems.
- Solar Energy Community (DLCS) in Transma, South Africa: combines solar and geothermal energy through pre-insulated piping systems to provide energy to the community.
- Other cases:
- JW Marriott Guanacaster Resort Costa Rica, USA: Use Urecon’s pre-insulated piping system to provide a cooling water distribution system for the resort.
- Port Authority of Singapore, Sydney Dabolam, Port Moresby Pettier Bay: Insafoam’s pre-insulated piping system is used for hot water supply and cooling.
These cases demonstrate the widespread use of pre-insulated pipelines in different scenarios, from residential and commercial buildings to large public facilities and industrial applications, which can effectively improve energy efficiency, reduce energy losses, and reduce long-term operating costs.
With a service life of 30 years, the aging and maintenance requirements of pipeline materials are as follows:
- Pipe material selection:
- Metal pipes: such as steel pipes and cast iron pipes, usually have a lifespan of more than 30 years under good corrosion protection conditions. However, if corrosive water, improper installation or maintenance are present, its lifespan may be shortened. Anticorrosion coatings or resin linings are recommended for extended service life.
- Plastic pipes: such as PVC and PE pipes, usually between 20 and 50 years, depending on the material quality and use environment. High temperature, high humidity and internal pressure environments will accelerate aging. Regular inspection and maintenance are recommended to prevent leakage and damage.
- Copper tube: It has a long service life, usually over 50 years, but requires regular inspection and maintenance to prevent corrosion and leakage.
- Aging and maintenance strategies:
- Regular inspection: Regularly check the pipeline for signs of leakage, corrosion, deformation, etc. Detecting and handling these problems in a timely manner can extend the service life of the pipeline.
- Cleaning and Maintenance: Regularly clean sediment and dirt inside the pipe to prevent clogging and corrosion. For plastic pipes, avoid overheating and UV exposure.
- Anti-corrosion treatment: Perform regular anti-corrosion treatment on metal pipes, such as coating anti-corrosion coatings or cathodic protection, to improve their corrosion resistance.
- Replace aging parts: Replace aging or damaged pipe parts, such as valves, joints, etc. in a timely manner to prevent leakage and other problems.
- Maintenance in special environments:
- High temperature environment: In high temperature environment, the physical and chemical properties of pipeline materials will undergo significant changes, accelerating aging. It is recommended to use high-temperature resistant materials and conduct regular inspection and maintenance.
- High pressure environment: In high pressure environment, the strength and sealing performance of pipeline materials will be affected. It is recommended to use high-strength materials and perform stress testing regularly.
- Comprehensive management:
- Establish a complete pipeline management system: including the collection and analysis of operational data, the establishment of maintenance records, and the monitoring and evaluation of aging and corrosion.
- Adopt new technologies and new materials: New technologies, new processes, new materials and new equipment are adopted in design and construction to improve the reliability and safety of the pipeline system.
Through the above measures, the service life of the pipeline can be effectively extended and ensure that it maintains good operating conditions within 30 years of service life.